Chemicals 4.0 – An Overview of Potential Digitization Drivers
Published on 15 Jan, 2021
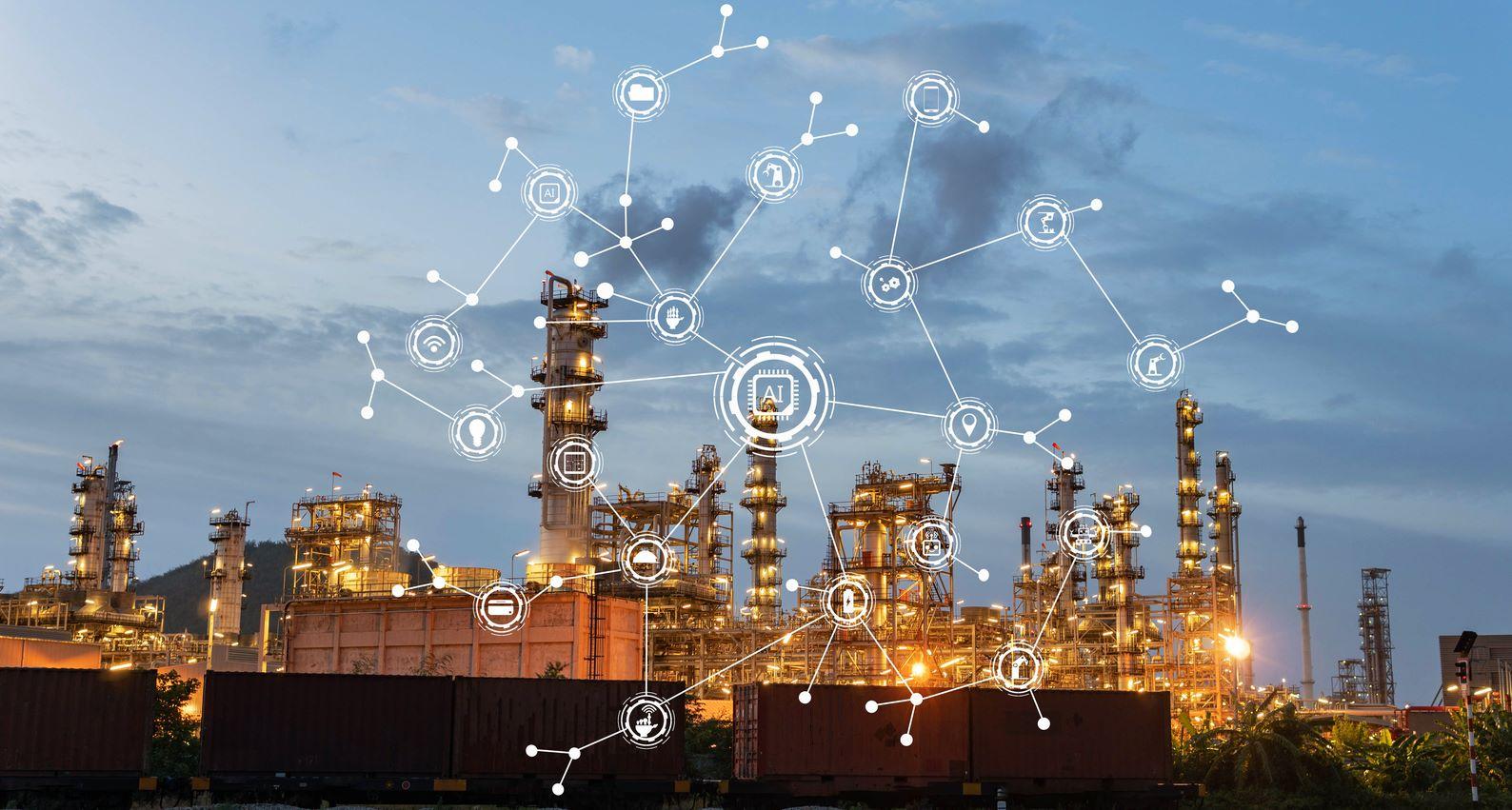
Parallel to the industrial revolution, the chemical industry has surged in terms of both production volumes and innovations. The sector’s adaptability to modernization, especially adopting digitization, is a testament to its resilience, irrespective of economic conditions, especially the crisis currently underway globally. Considering the innovations, investor interest, and positive industry estimates, digitization in this sector is expected to increase. Due to the constant need for chemicals across allied and non-allied sectors, the outlook for the chemical industry would continue to be positive. Hence, along with the trending ‘Industry 4.0,’ ‘Chemicals 4.0’ must concord, paving the way for the potential adoption of several digitization drivers.
Historically, the chemical industry has incorporated nearly all digital innovations relevant across industries. Digitization in the chemical industry would primarily influence:
Productivity and efficiency – Increasing competitive advantage and lowering costs through optimized operations
Innovations – Boosting productivity in R&D to reduce time to market
Data management and analysis – Improving product development via customer insights to optimize offerings
Workforce – Transforming tasks, opportunities, and job requirements
Offerings – Digitally enhancing product performance, especially for close-to-end-customer markets
We explore a few leading technology drivers that have potential to boost digitization in this sector.
Modeling and Simulation
Computer-based modeling and simulations were initially implemented in the 1970s to partially automate chemical processes. Currently, computational models are being increasingly researched and published year-on-year. Several novel reactions are being predicted mathematically. In particular, modeling can help predict conditions for conducting high/sub-zero temperature experiments at ambient temperatures, as well as facilitate drug discovery. Furthermore, extensive R&D on computational fluid dynamics continues to benefit the chemical industry.
The energy industry is a key deployer of computational simulation technologies. Recently, ABB and CORYS collaborated to deliver advanced twin technology systems to enhance control monitoring and process modeling simulations for energy and process industries. Computational simulations, especially molecular modelling, have key applications in the allied pharma industry. As per Data Bridge Market Research, the global molecular modelling market will likely expand by a CAGR of 15.25% during 2019–26.
Collaborative Robots (Cobots)
Cobots have aided growth in all industrial verticals since the past two decades. These are typically deployed separately or in tandem with workers to enable safe, efficient, and optimized operations in factories. In the chemical industry, cobots have the potential to be programmed for aiding processes conducted at high temperatures or in physically/chemically hazardous environments that are deemed unsafe for workers.
Cobots have potential to be deployed for material handing in the chemical industry. As per Global Marketers, the market for material handling cobots would expand during 2019–26. Human-cobot interactions need to be effective for optimized operations. Hence, employees need to be well-trained for handling cobots. Recently, a UK-based cobot manufacturing company set up a first-of-its-kind authorized training center in collaboration with a Danish robotics firm. The center aims to help improve human-robot interactions, and consequently, enhance production efficiency.
Artificial Intelligence (AI)
Since the past decade, AI-based technologies are being gradually immersed in the chemical industry. Owing to their capability to mimic human cognitive functions, especially learning and problem solving, these technologies can help expedite innovations, reduce costs, increase operational efficiency, and improve customer satisfaction. Hence, AI has the potential to design efficient ‘idea-to-market’ strategies.
AI-based technologies appear to have already been beneficial in enhancing processes post implementation. As per a survey by Accenture, until 2018, about 72% of chemical companies adopting AI-based technologies witnessed a minimum two-fold enhancement in few processes, while 37% companies recorded five-fold enhancement. At present, research centers are needed for accelerating AI-based innovations in the chemical industry worldwide. Recently, LivNSense Technologies and ARITAR collaborated to launch a Center of Excellence in India to encourage such innovations to boost growth in the petrochemical industry. AI-based technologies for environment remediation are currently being developed, particularly for lowering carbon footprint. PwC UK estimates greenhouse gas emissions would drop 4% by 2030 on adopting AI in key industries, including water and energy.
Internet of Things (IoT)
The IoT has recently found acceptance in the chemical industry, with its advantages being similar to other digitization drivers in the lines of improving productivity and boosting profitability. With the help of inexpensive computer chips and ubiquitous wireless networks, factory equipment can be linked to a virtual interface. This would help manufacturers identify and repair/replace poor performing equipment; rapidly detect and track quality issues; monitor end-to-end chemical processes; and customize processes as per customer requirements.
The significance of the IoT continues to grow in the chemical industry. As per MarketIndustryReports, globally, the IoT in chemical industry market was estimated to be valued at USD39 billion in 2018, with anticipation of healthy CAGR expansion during 2019–30. Such growth in IoT adoption would concurrently boost growth in the market for batteries to operate IoT devices. Numerous established and new companies have recently launched high-lifecycle batteries, especially catered to IoT devices.
Big Data
As with other industries, big data has potential to revolutionize all aspects of the chemical industry, including end-to-end upstream and downstream processes, product development, supply chain management, and marketing. Specifically, big data would positively impact the following aspects of the chemical industry:
Production – Real-time decision-making on asset utilization and process scheduling
Supply Chain – Data integration to streamline processes and enhance distribution networks
Safety – Determining the root cause of factory incidents to develop long-term remedies and prevent reoccurrence
Pricing – Analyzing profitability, market forecasting, and raw material availability to optimize pricing policies
R&D – Collating data from customers, forecasts, and market trends for customized product development Adoption of big data would primarily rely on the outlook for chemical software required for its implementation. ReportLinker recently stated that the global chemical software market would be valued at USD192.36 million, expanding by a CAGR of 5% during 2020–24. Data historian solutions are also relevant to big data’s implementation for the efficient collection of data from industrial systems (e.g., SCADA). The data historian solutions market would expand at a CAGR of 5% to USD1.3 billion by 2025 from USD1.1 billion in 2020, as per MarketsAndMarkets.
Deployment Challenges and Outlook
The technologies discussed above are the most relevant among many drivers of digitization in the chemical industry. That being said, several challenges exist, particularly related to deployment and investments in such innovations.
Value proposition – Most digital innovations are recent, and offerings are constantly being upgraded owing to intense competition among technology players. This causes uncertainties in choosing the appropriate technology for implementation in chemical plants. Therefore, chemical companies may face challenges in presenting a concrete value proposition for justifying investments in digitization.
System integration – Big data is considered a boon to the industry. However, its implementation is easier said than done, as vast quantities of historical and current data need to be stored and processed. Hence, it may take several more years to reap the fruits of big data. Many issues also mar the application of the IoT, especially with regard to seamless integration with operational equipment and abnormal faulting in real time.
Cybersecurity – Progress in digitization has simultaneously surged internet connectivity globally. Naturally, cybersecurity continues to be a challenge, with emphasis being on IP protection. Only few countries have stringent IP and cybersecurity laws/regulations, which pile on to the challenges presented by digitization to chemical companies.
Employability – The chemical industry is undoubtedly among the top employers globally. Over 10 million employees currently work in this sector, with millions of others being indirectly involved in allied industries. Industrial digitization, particularly automation, could result in workforce reduction. However, this might be majorly offset by increasing employment within digitization roles. Nevertheless, digitization presents the challenge of constantly upskilling employees and increasing their engagement with technologies, all of which are time- and cost-intensive.
Environment – Environment remediation is among the key outcomes expected from digitization. Conversely, these technologies negatively affect the environment while being produced or deployed. While data is considered the new oil, technologies used for data processing may affect the environment in the same manner as fossil fuel refinement and consumption. MIT Technology Review reports that training just one AI model can cause carbon emission equivalent to that produced by five cars in their lifetimes.
Despite the challenges faced, digitization is deemed to be key in the positive outlook for the chemical industry. As per a survey conducted by Siemens, 48% of chemical companies expect ROI on digitalization-based innovations within two years, while only 10% estimate ROI in over five years. Moreover, digitization has the potential to enhance the value delivered by employees in chemical companies. Accenture stated that optimal digitization initiatives would increase operational efficiency and save about USD91,000 per chemical company employee (global average).
Plausible process flow using leading digitization drivers
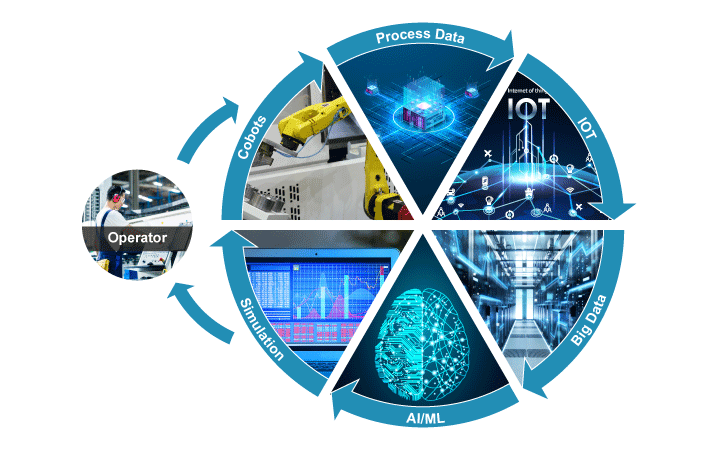
Conclusion
Several digitization drivers have made a mark and continue to positively impact both the demand side (chemical companies) and supply side (technology providers). Most of these technologies, despite their uniqueness, have similar positive outcomes as discussed above. Hence, their holistic implementation by chemical companies would be unsurprising. In addition to process improvements and higher revenues, digitization has the potential to boost sustainability and circular economy, which are of prominence in this sector. With the ongoing global crisis waning as we enter the new year, chemical companies need to adopt appropriate digital technologies to drive robust growth.