Can Technology Help Mitigate Semiconductor Shortage?
Published on 20 Dec, 2021
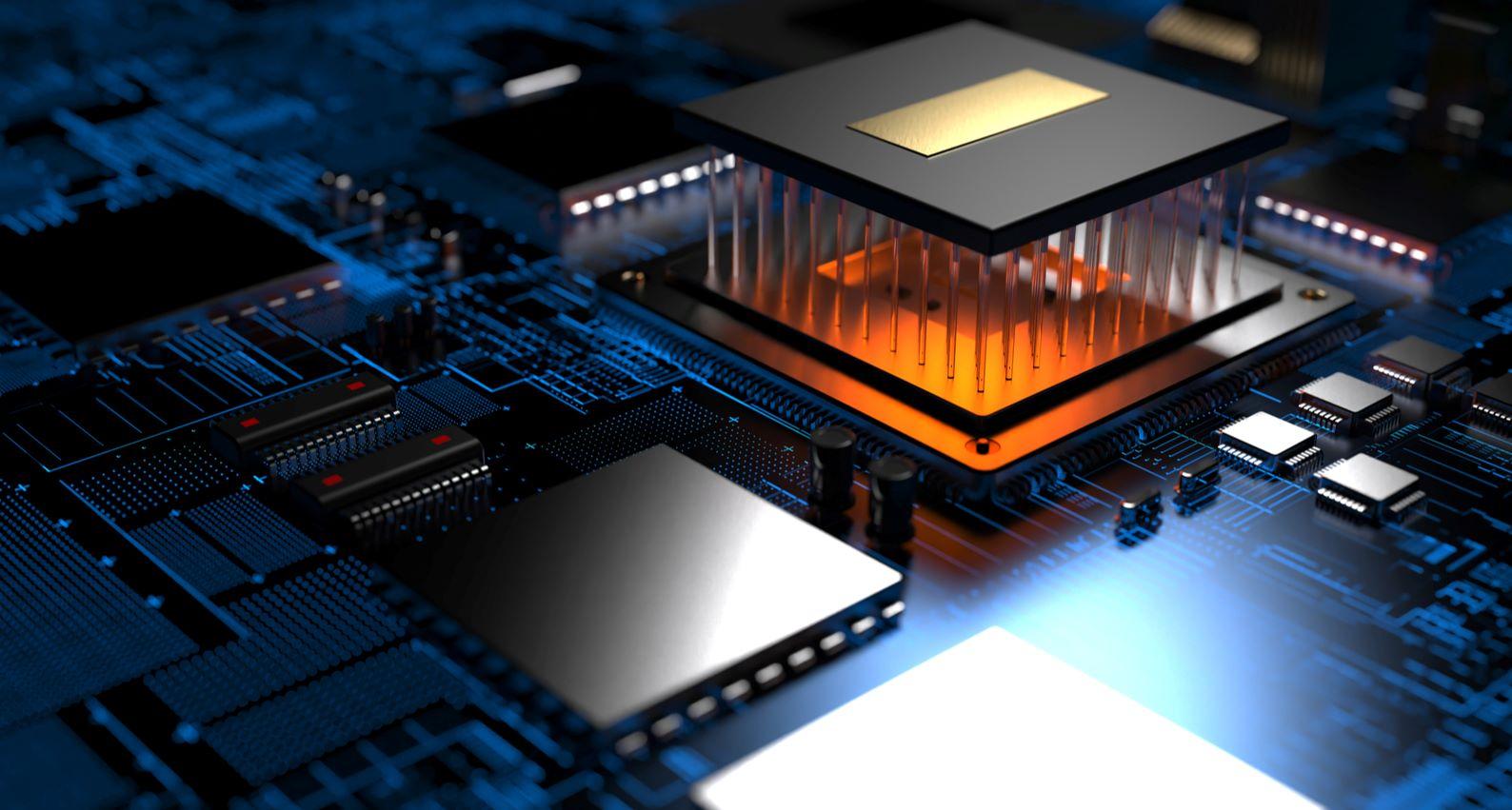
COVID-19 adversely impacted many industries, one of which is the semiconductor industry. The global shortage of this critical raw material had a cascading effect on the automobile and electronic industry. While the solution is to increase production, it is difficult to manufacture semiconductors. However, technologies such as Artificial Intelligence (AI) and Internet of Things (IoT) and new innovations can help the industry optimize production and fill the void created.
The global shortage of semiconductors or smart chips is affecting the electronics and automobile industry. Although small in size, semiconductors are an important component of any electronic device and perform a host of functions such as powering displays and transferring data. They are a critical raw material, and a crunch in their supply chain negatively impacts the automobile and electronics industry.
The main reasons for this shortage are as follows:
- Pandemic effect - COVID-19 resulted in lockdowns and productions delays across the world. In this period, the demand for electronics such as gaming consoles, phones, and laptops soared due to the work-from-home (WFH) model and forc¬ed isolation, leading to a surge in the demand for consumer electronics.
- Electrification - Increasing electrification of vehicles and rising demand for semiconductor chips is causing a demand–supply imbalance.
- Automobile industry – Lack of demand in the beginning of 2020 led to the auto industry dropping its manufacturing capacity. However, as new-vehicle sales grew in the second half of the year, automakers faced shortage of semiconductors as they reduced their raw material requirement and did not order for increased manufacturing.
- Geopolitical tension – Strained relationship between the US and China resulted in Chinese companies such as Huawei, which supplied semiconductor to US chip makers, being blacklisted by the US government. Currently, US companies have limited supply of semiconductors.
- Demand for upcoming technologies – Semiconductors are required for many emerging technologies such as 5G rollout and implementation of AI in automobiles. While 5G rollouts require many radio-frequency semiconductors, power-electronic chips are needed for cars using AI, particularly in advanced driver-assistance systems (ADAS), LiDAR, and safety and convenience functions.
Furthermore, COVID-19 led to increased digitization, which boosted the demand for semiconductors. The need for advanced chips or semiconductors for 5G upgrade, AI, machine learning, and cloud computing will continue to drive demand.
While companies are on a war footing to increase production, it is difficult to manufacture semiconductors on a short notice.
Technologies to the rescue
The issue of semiconductors can be resolved by applying technology in the manufacturing process of chips. Some emerging technologies that can be used are as follows:
Artificial Intelligence (AI) – The new-age technology of AI can be applied to legacy equipment of the last 20 years to manufacture semiconductors although not as per the established pattern. Therefore, older machines can be used to make chips for optimized production and better yields. The many benefits of AI are as follows:
- AI can help reinvent the inspection process. It allows the implementation of predictive systems to continuously scan for defects in real time, thereby improving product quality while reducing wastage.
- AI allows alignment with manufacturing at the highest level of detail possible, enabling minute wafer-level inspection.
- New material development and device designs are enhanced when paired with AI and computation.
Mixed Integer Linear Programming (MILP) – A start-up from London, Flexciton introduced a new mathematical technique called mixed integer linear programming (MILP), which is a notch above some machine learning techniques. It finds a better factory scheduling solution within 15 minutes, which is extremely useful for highly dynamic, modular manufacturing lines used for semiconductors.
A Northern Ireland company, Seagate implemented MLIP and achieved 10% improvement in efficiency in a proof-of-concept project. It has rolled out this system for 60% of the machines. Flexciton increases efficiency by reducing the time taken to produce each semiconductor by 7% to 10%, which would mean USD3–5 million in savings per month.Internet of Things (IoT) – Integration of IoT with business processes can provide a unified view of production as well as end-to-end supply chain. Most industrial IoT platforms integrate their diverse systems, sensors, and software into one centralized system to get the complete picture. Semiconductor manufacturers can use this visibility for intelligent information gathering, analyzing, and creating action points for multiple processes that were previously in siloed applications. Insights derived from the data help in demand forecasts, inventory, scheduling, and production across the supply chain.
IoT can help implement enterprise resource planning (ERP), customer relationship management (CRM), and sophisticated IoT assets. IoT provides complete visibility to a manufacturing unit to manage its supply chain elements at the right time.
Other considerations for leaders
While semiconductor companies can use technologies to optimize their production, industry leaders must also focus on the following:
- Equipment upgrades – Chip manufacturing units must upgrade to new equipment over a long period. However, even if floor space is available, the process of procuring and installing new equipment will not enhance production capacity quickly to address the demand surge. The equipment build lead time increases due to fluctuation in raw material availability. The option to upgrade hardware or software of existing equipment is provided to help achieve improved throughput or new capabilities over various manufacturing stages.
- Prioritization – Until the semiconductor shortage crisis ends, chip manufacturers should prioritize its production and reduce non-production activities. The team can also eliminate or delay certain engineering lots that consume capacity. Time required for semiconductor manufacturing at different stages (final test, wafer sort, burn-in test, etc.) can also be reduced without losing quality.
- Asset utilization – Semiconductor companies must also ensure optimal utilization of assets. For instance, operator allocation and scheduling can be refocused to reduce tool assist response times. This will allow availability of tools at critical times and enhance overall production.
Conclusion
Semiconductor shortage is expected to continue for the next few years and will negatively impact the automobile and electronics industry. Leveraging emerging technologies to increase production could help resolve the situation faster but they need to be integrated intelligently and quickly. Unless concrete steps are taken in this direction, it will be difficult to resolve the issue of shortage.