Navigating Supply Chain Shifts in Fastener Industry
Published on 15 Feb, 2024
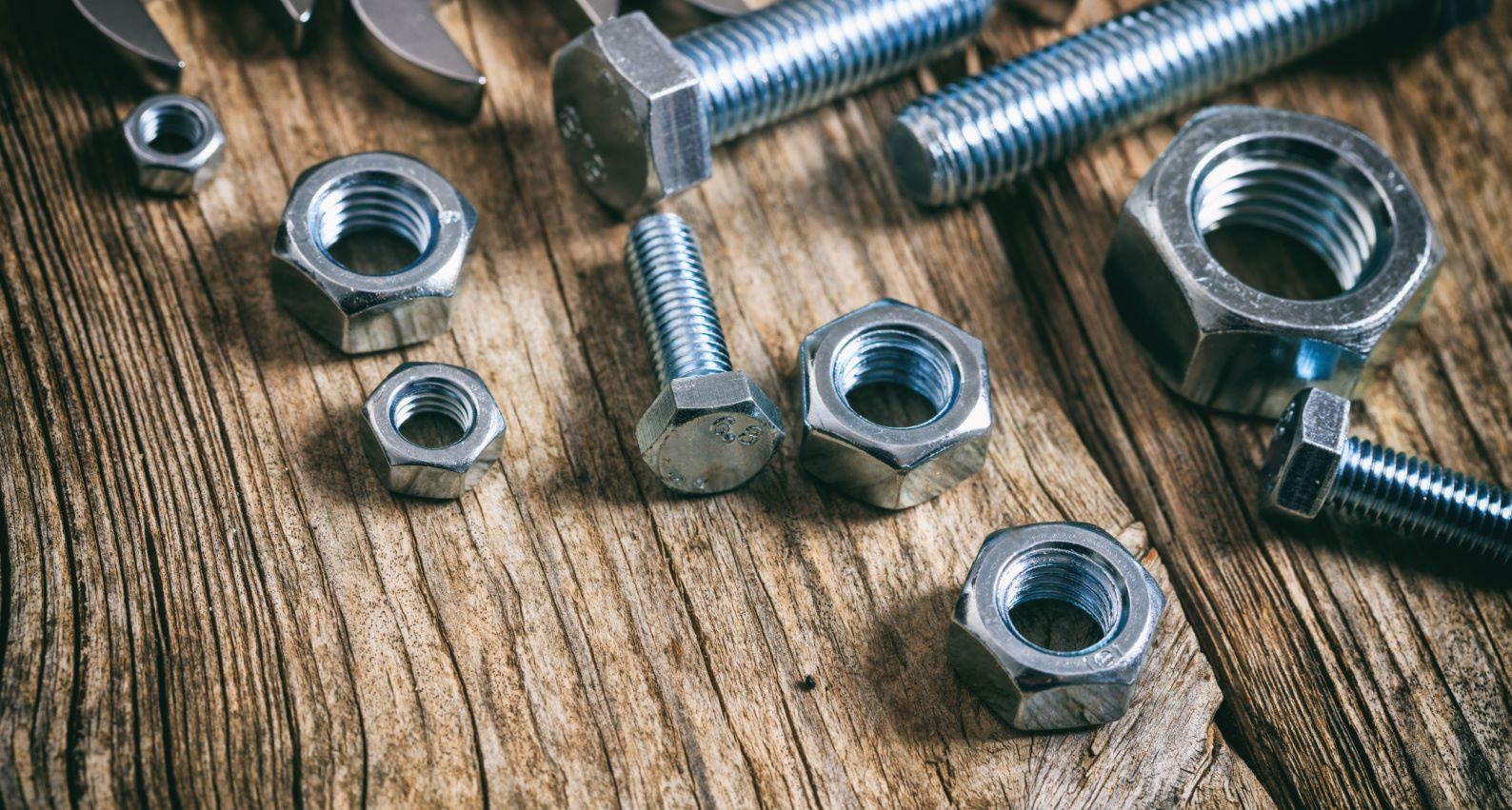
Fasteners traverse a large and interconnected global supply chain due to their applicability across industries. The rise of supply hubs worldwide has significantly impacted the dynamics of fastener supply. The global strategy is leaning toward offshoring to Asia-Pacific (APAC) countries such as India and Taiwan, specifically as alternatives to China (China Plus One), for realizing cost advantages and enhancing supply chain resilience. Nearshoring, however, is gaining traction in North America and Europe for addressing supply chain downtime concerns and logistics inefficiency.
India is emerging as a close competitor of China in the offshoring model, which is preferred for building supply chain resiliency and supporting the China Plus One strategy.
Different regions have developed specialized capabilities in fastener production based on their industrial strengths and expertise. For instance, Asia, with a focus on China, Taiwan, and India in particular, has become a major hub for mass production of standard fasteners (such as square and hex bolts, screws, nuts, studs, and rivets) due to cost-effective manufacturing. On the other hand, Europe focuses on high-precision and specialized fasteners for critical applications in the aerospace and defense industry. This is reflected in the regional production costs as manufacturers adhere to higher quality standards, which may incur additional costs and thus impact the overall price of the fasteners.
The availability and cost of raw materials play a significant role in influencing fastener prices. For instance, regions with access to abundant raw materials, such as steel and aluminum, can produce fasteners more competitively. Moreover, supply hubs with proximity to raw material sources have a cost advantage over those relying on extensive transportation.
Labor costs and skill levels in a particular region impact the overall cost of production. For instance, APAC countries with lower labor costs may have a competitive edge in mass production. In contrast, regions with high labor costs due to highly skilled labor may excel in precision and complex fastener manufacturing. This creates a diverse landscape of supply hubs catering to different market segments.
Typically, for fastener production, the cost of raw material is the largest component, accounting for 40-60% of the total costs. This is followed by labor cost at 10-30%, depending on the geography. The cost of other expenses toward utilities, coatings, testing, packaging, etc., accounts for the rest.
In the APAC region, China, Taiwan, and India are the largest supply hubs for fasteners with a total regional base of 500+ suppliers. With abundant domestic raw material supply and cheap labor costs, the APAC market offers an attractive prospect to source low-cost fasteners globally. While China and Taiwan have been traditional hubs for global fastener exports, India has emerged as a fierce competitor in terms of quality and costs. Despite China offering steel that costs 10–20% less, India’s competitive labor costs across APAC make it a suitable alternative for buyers opting for China Plus One strategy.
Preference for nearshoring from North America and Eastern Europe to increase logistics efficiency
The cost of transporting fasteners from manufacturing hubs to end-users significantly contributes to price differences. Prices of fasteners are highly competitive in regions with effective logistics networks and proximity to major markets, due to reduced logistics costs. Thus, preference is given to nearshoring from North America and Europe, to reduce supply chain downtime.
In North America, the US and Canada account for 100–120 suppliers in the fastener supply market. Mexico has fewer fastener suppliers, despite its large automotive industry. However, American raw material and labor costs are higher than APAC’s. Hence, the overall fastener production costs in America are typically higher by 50-100% compared to those in APAC.
In Europe, key fastener supply hubs are split between Western Europe (Germany, France, Italy, and the UK) and Eastern Europe (Hungary, Poland, Czech Republic, and Turkey). Fasteners are typically expensive in Western Europe, 100–150% higher than APAC prices. Hence, East European suppliers are more cost-effective for the region, with prices 35–75% higher than APAC prices. However, the overall fastener production in Europe is lower compared to its Asian and American counterparts, primarily due to the high production costs. Hence, leading buyers prefer sourcing from APAC markets to cater to their requirements.
In conclusion, fastener prices are primarily controlled by the regional variation in their raw material prices and other factors such as labor, ESG, logistics, and packaging costs. India is well positioned to compete with China’s low-cost market leadership in the fastener supply chain offshoring model, with European and American buyers either relying on APAC-based imports to optimize their spending on fastener sourcing or nearshoring from suppliers based in Mexico and Eastern Europe.